Juni 19, 2024
Wie und wieso Software-defined Manufacturing die Industrie verändert
Die Zukunft der Produktion liegt in digitalen, automatisierten Prozessen. Nur so können Unternehmen flexibel werden und sich unabhängiger machen von spontanen Marktentwicklungen und Fachkräftemangel. Software-defined Manufacturing (SDM), heißt die Entwicklung, die dieser Änderung der Produktionsbedingungen zugrunde liegt. Der zentrale Unterschied zu konventionellen Methoden: Die Software und softwaregestützte Technologien stehen im Mittelpunkt der Fertigungsprozesse.

SDM verspricht eine effizientere Produktionsweise und erhebliche Steigerung der Anpassungsfähigkeit von Fertigungslinien. Auch Innovationen und neue Geschäftsmodelle lassen sich in einer Sofware-zentrierten Produktionsumgebung schneller vorantreiben.
Die Grundlagen des Software-defined Manufacturing (SDM)
Beim traditionellen Fertigungsansatz steht die Hardware mit Maschinen und Anlagen im Mittelpunkt und wird ebenfalls durch eine Hardware, nämlich die SPS, gesteuert. Im Software-defined Manufacturing ersetzen Unternehmen dieses Konzept. Sie steuern die Hardware, also auch die SPS, über dynamische Softwaresysteme oder Softwareplattformen. Sie optimieren so die Hardware und damit die gesamte Fertigungskette. Der große Vorteil: Unternehmen können so auf Marktveränderungen fast in Echtzeit reagieren, da im Software-defined Manufacturing Anpassungen an neue Anforderungen und Designs wie auch Änderungen in Produktionsprozessen durch Softwareupdates statt physischer Umbauten erfolgen können. SDM integriert digitale Schlüsseltechnologien wie das Internet of Things (IoT, Internet der Dinge), Cloud-Computing und künstliche Intelligenz (KI).
Die Rolle der IT-OT-Konvergenz
Die Konvergenz von Informationstechnologie (IT) und operationeller Technologie (OT) spielt eine zentrale Rolle im Software-defined Manufacturing. Diese Konvergenz führt zu einer nahtlosen Integration von Daten- und Steuerungsflüssen zwischen administrativen und produktionsbezogenen Bereichen eines Unternehmens, zwischen Büro und Produktion. Durch die Integration von IT- und OT-Systemen können Daten aus der Produktion in Echtzeit erfasst und analysiert werden. Das erhöht die Transparenz und führt zu präziseren und fundierteren Entscheidungen. Die Konvergenz ermöglicht es Unternehmen, Probleme in der Produktion zu antizipieren, bevor sie auftreten oder wenn sie auftreten, dann schnell darauf zu reagieren und sie zu beheben, bevor sie zu größeren Störungen führen. Die IT-OT-Konvergenz fördert die Entwicklung von prädiktiven Wartungsstrategien, was wiederum die Betriebszeiten erhöht und ungeplante Ausfälle reduziert. Darüber hinaus können durch die IT-OT-Konvergenz Effizienzsteigerungen und Kosteneinsparungen erzielt werden, da redundante Systeme und Prozesse eliminiert werden. Die Integration von IT und OT ist ein entscheidender Schritt hin zu einer vollständig vernetzten und intelligenten Produktionsumgebung, die die Grundlage für die Fabrik der Zukunft bildet.
Hyperkonvergenz in der Fertigung
Hyperkonvergenz erweitert die Idee der Konvergenz, indem sie Speicher-, Rechen- und Netzwerkoperationen in einer einzigen, vereinheitlichten Systemarchitektur zusammenführt. Dadurch können Unternehmen ihre IT-Landschaft vereinfachen und zentral verwalten. Dies reduziert nicht nur den Verwaltungsaufwand, sondern erhöht auch die Flexibilität und Reaktionsfähigkeit der Produktionssysteme. Datensilos werden aufgehoben, verflochtene Steuereinheiten entkoppelt.
Hyperkonvergenz ermöglicht es, schnell auf Veränderungen in der Produktion zu reagieren, indem Ressourcen je nach Bedarf dynamisch neu zugewiesen werden können. Dies ist besonders in Umgebungen mit wechselnden Produktionsanforderungen von Vorteil, da Unternehmen so schneller und effizienter auf neue Marktanforderungen reagieren können. Die Systeme sind hochgradig modular und lassen sich leicht an veränderte Produktionsbedingungen anpassen.
Im Einsatz bei Fertigungsunternehmen können hyperkonvergente Systeme die IT-Footprints reduzieren und gleichzeitig die Leistung und Kapazität steigern. Die zentrale Verwaltung von Ressourcen durch eine hyperkonvergente Infrastruktur verbessert die Reaktionsfähigkeit auf Anforderungen aus dem Produktionsprozess und sie erleichtert die Implementierung fortschrittlicher Analytik, die zur Optimierung des gesamten Fertigungsprozesses beiträgt.
Use Case: SDM in der Stuttgarter Maschinenfabrik
Welche Möglichkeiten SDM in der Praxis bietet, haben wir erfolgreich in der Stuttgarter Maschinenfabrik des ISW (Institut für Steuerungstechnik der Werkzeugmaschinen und Fertigungseinrichtungen) umgesetzt. Die Prozessorchestrierung von Maschinen und AGVs (Automated Guided Vehicles) erfolgt herstellerunabhängig über digitale Zwillinge. Die hochparallele und hochperformante Kommunikation zwischen den digitalen Zwillingen untereinander sowie zwischen ihnen und den Maschinen und IT-Systemen wird über Standardprotokolle (OPC UA, REST etc.) organisiert. Produkt, Prozess und Ressourcen sind miteinander verlinkt und flexibel änderbar. Interaktionen werden ereignisdiskret geloggt, damit man volle Transparenz und Flexibilität hat. Da die Daten in ihrem jeweiligen Kontext erfasst werden, stellt das auch einen idealen Hebel für KI-basierte Optimierungen dar. Das Monitoring erfolgt über eine Echtzeit-Visualisierung des Prozesses im NVIDIA-Omniverse. Damit realisiert Ascon Systems in SDM4FZI eine voll ausgebaute und mächtige Industrial-Metaverse-Anwendung.
Der Use Case zeigt, dass man mit Software-defined Manufacturing noch weitere Vorteile für sich erschließen kann. Der Prozess kann online geändert und er kann remote und in Echtzeit visualisiert werden. Zur Visualisierung wird im Use Case die 3D Plattform NVIDIA Omniverse verwendet. Genauso ist es aber beispielsweise möglich, einem Mitarbeitenden vor Ort alle notwendigen Informationen zum Zustand der Anlage oder Wartungsinformationen auf sein Tablet zu spielen. Terminals und Papiere entfallen. Damit wird es möglich, die Vorteile des Software-defined Manufacturing an sich, und auch die Potenziale beim Refit von Brownfield-Umgebungen zu zeigen.
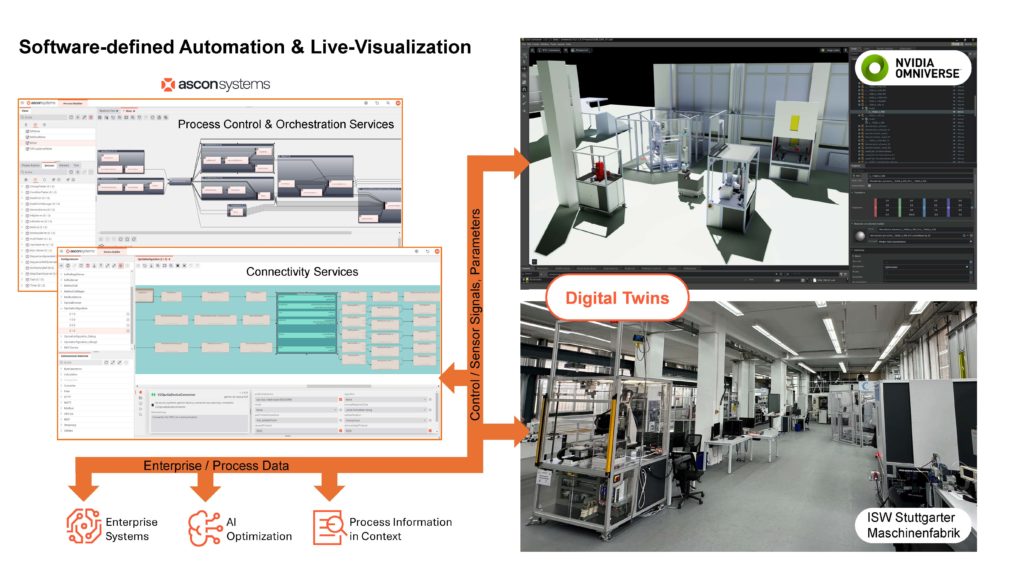
Ascon Systems SDM4FZI-Demonstrator mit 3D
Dieser und andere Use Cases zeigen die vielfältigen Nutzungs- und Einsatzmöglichkeiten von Software-defined Manufacturing. Sie sind ausführlich auf der Webseite des Projekts https://www.sdm4fzi.de beschrieben.
Basis für die Software-defined Factory – die Fabrik der Zukunft
Die „Fabrik der Zukunft“ wird durch Technologien wie SDM möglich gemacht. Diese hochautomatisierten und flexiblen Produktionsstätten nutzen vollständig die Vorteile der digitalen Steuerung, um schnell auf Marktveränderungen und individuelle Kundenanforderungen zu reagieren. Hierbei spielen Robotik, erweiterte Automatisierung, künstliche Intelligenz (KI) und maschinelles Lernen eine entscheidende Rolle, weil sie die Effizienz steigern und Fehlerquoten reduzieren. In der Fabrik der Zukunft sind alle Systeme und Maschinen miteinander vernetzt und werden zentral überwacht und gesteuert. Dies ermöglicht eine kontinuierliche Optimierung der Produktionsprozesse und eine schnelle Anpassung an neue Anforderungen. Durch den Einsatz von Sensoren und vernetzten Geräten können Daten in Echtzeit erfasst und analysiert werden, um Produktionsprozesse zu verbessern und die Qualität zu steigern. Diese Fabriken sind effizienter und zugleich nachhaltiger, weil der Einsatz von Material und Energie optimiert wird. Darüber hinaus wird die Arbeitsumgebung sicherer und ergonomischer, da viele gefährliche oder monotone Aufgaben von Robotern übernommen werden. Die Fabrik der Zukunft repräsentiert einen Paradigmenwechsel in der Fertigung, der durch die Integration von SDM und anderen fortschrittlichen Technologien ermöglicht wird.
Aktuell untersucht ein Forschungsverbund aus Wissenschaft und Wirtschaft – in dem auch wir beteiligt sind – in dem öffentlich geförderten Projekt „SDM4FZI – Software-defined Manufacturing für die Fahrzeug- und Zulieferindustrie“, die Potenziale für Software-definierte Fertigung in den Branchen Automobil- und Zulieferindustrie. Das Projekt wird Ende 2024 abgeschlossen, erste Ergebnisse gab es schon vorher, bei den Stuttgarter Innovationstagen am 17. und 18. September 2024 zu sehen.